Water bottles are an essential part of daily life for millions of people worldwide. Whether you’re an athlete, office worker, student, or traveler, a reusable water bottle provides an eco-friendly, cost-effective, and convenient way to stay hydrated. However, as their popularity grows, so do concerns about the safety and compliance of these products. Manufacturers, retailers, and consumers alike must prioritize ensuring that water bottles meet strict safety and compliance standards to avoid potential health risks and regulatory violations.
This guide provides an in-depth look into how to ensure product safety and compliance in water bottles, covering materials selection, regulatory requirements, testing, and best practices for manufacturing and marketing.
1. Understanding Product Safety Standards for Water Bottles
Ensuring product safety begins with understanding the regulations and standards governing water bottles in your target market. These standards vary by region and are often enforced by government agencies or independent organizations.
a. Key Regulatory Bodies and Standards
- United States: The Food and Drug Administration (FDA) oversees water bottle safety, ensuring that materials used are food-safe and free from harmful substances like Bisphenol A (BPA).
- European Union: The EU’s Regulation (EC) No 1935/2004 mandates that materials in contact with food or beverages do not transfer harmful substances.
- China: GB 4806.7-2016 is the national standard for plastic materials used in food contact.
- Other Standards: Organizations like NSF International and ASTM International set voluntary standards for water bottles, focusing on safety, durability, and functionality.
b. Common Safety Concerns
- Chemical Leaching: Some materials may release harmful chemicals into the water, especially when exposed to heat.
- Microbial Contamination: Poor design or materials can lead to bacteria growth inside the bottle.
- Durability Risks: Substandard bottles may crack or break, leading to physical hazards.
2. Choosing Safe and Compliant Materials
The choice of materials is critical to ensuring water bottle safety and compliance. Different materials come with their own safety profiles, benefits, and drawbacks.
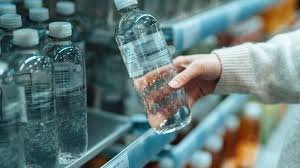
a. Common Materials Used in Water Bottles
- Plastic (e.g., Tritan, Polypropylene)
- Lightweight, durable, and affordable.
- Look for BPA-free and FDA-approved plastics.
- Stainless Steel
- Non-reactive, durable, and resistant to corrosion.
- Ensure the use of food-grade stainless steel, such as 18/8 or 304 stainless steel.
- Glass
- Non-toxic and non-porous.
- Fragile and requires additional safety measures like protective sleeves.
- Silicone (for parts like lids or sleeves)
- Flexible, durable, and heat-resistant.
- Must meet food-grade standards.
b. Avoiding Hazardous Materials
- Bisphenols (BPA, BPS): Known endocrine disruptors that can leach into water.
- Phthalates: Found in some plastics, they can pose health risks with prolonged exposure.
- Lead and Heavy Metals: Often found in paints or coatings, these are highly toxic.
3. Testing and Certification Processes
Comprehensive testing is essential to verify that water bottles meet safety and compliance standards. Manufacturers should work with accredited laboratories to perform these tests.
a. Types of Tests
- Chemical Testing
- Ensures materials do not leach harmful substances.
- Common tests: BPA testing, heavy metal analysis, and overall migration tests.
- Durability Testing
- Assesses resistance to impact, pressure, and temperature fluctuations.
- Microbial Testing
- Evaluates whether the design and materials promote bacterial growth.
- Thermal Testing
- Verifies performance under hot or cold conditions.
b. Certification Programs
- NSF Certification: Focuses on material safety and performance.
- FDA Compliance: Necessary for food and beverage-related products sold in the U.S.
- LFGB Certification: Indicates compliance with German food safety standards.
- CE Marking: Required for products sold in the European Economic Area (EEA).
4. Designing for Safety and Compliance
The design phase is crucial in minimizing safety risks and ensuring compliance. A well-designed water bottle can enhance usability while adhering to safety standards.
a. Key Design Considerations
- Ergonomics: Ensure the bottle is easy to hold, open, and clean.
- Leak-Proof Design: Use high-quality seals and testing to prevent leaks.
- Hygienic Features: Incorporate wide openings for easy cleaning and antibacterial coatings if possible.
- Temperature Insulation: For thermal bottles, ensure the design maintains desired temperatures without compromising safety.
b. Sustainable and Eco-Friendly Design
- Use recyclable or biodegradable materials.
- Design for long-term use to minimize waste.
5. Manufacturing Best Practices
Ensuring product safety requires a robust manufacturing process that prioritizes quality control.
a. Quality Control Measures
- Material Verification: Ensure raw materials meet required standards.
- Batch Testing: Regularly test products during production to identify defects.
- Inspection Protocols: Perform visual and functional inspections to catch issues early.
b. Clean and Safe Production Facilities
- Maintain a clean manufacturing environment to prevent contamination.
- Train workers on safety and hygiene protocols.
6. Marketing and Consumer Education
Communicating the safety and compliance of your water bottles can build consumer trust and loyalty.
a. Transparent Labeling
- Clearly state certifications (e.g., “BPA-Free” or “FDA Approved”).
- Include care instructions to ensure safe use.
b. Educating Consumers
- Provide information on proper cleaning and maintenance.
- Highlight the benefits of safe materials and sustainable practices.
7. Staying Updated with Evolving Regulations
Regulations and consumer expectations are constantly evolving. Manufacturers must stay informed to maintain compliance and competitiveness.
a. Monitoring Regulatory Changes
- Subscribe to updates from regulatory bodies like the FDA, EU, or NSF.
- Join industry associations for insights on trends and standards.
b. Continuous Improvement
- Invest in research and development to create safer, more innovative products.
- Regularly review and update internal processes to align with new standards.
Conclusion
Ensuring the safety and compliance of water bottles is a multi-faceted process involving material selection, rigorous testing, thoughtful design, and transparent communication. By adhering to best practices and staying proactive about regulatory changes, manufacturers can produce water bottles that not only meet legal requirements but also earn the trust and loyalty of consumers.
In today’s market, where health and sustainability are top priorities, investing in safety and compliance is not just a legal obligation—it’s a competitive advantage.